Efficient, Scalable, and Cost-Effective Prefabricated Housing Solutions for Developers and Builders
As a developer or builder, speed, cost, and scalability are crucial to your success. Deepblue Smarthouse offers two seamless options to integrate prefabricated homes into your projects: choose from our proven standard designs or bring your own architectural plans for full customization. With 15 years of experience, we provide an efficient, cost-effective solution that helps you meet deadlines, stay within budget, and deliver high-quality results for your clients.
Step-by-Step Process for Developers and Builders
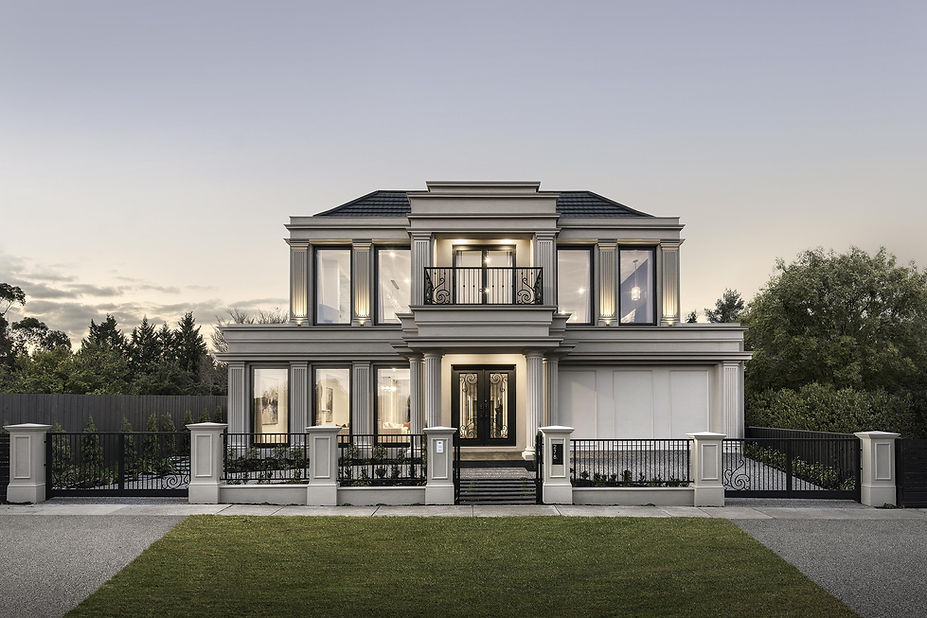
Option 1: Use Our Standard Design
Step 1: Explore Our Standard Designs
Step 2: Select Your Design
Choose the design that best suits your project's needs. With flexibility in customization, you can adjust layouts, materials, and finishes to match your specifications. We’ll ensure the design aligns with local regulations and site requirements.
Step 3: Receive Your Project Quote and Timeline
Once you select your design, we’ll provide a detailed quote that includes material costs, labor, and delivery. Our experienced team will also give you a clear project timeline to ensure your deadlines are met.
Step 4: Prefabrication and Delivery
We begin the prefabrication of the home in our advanced facility. With our streamlined production process, we can reduce on-site build time by up to 60%. After manufacturing, your homes are delivered to the site, ready for assembly.
Step 5: On-Site Assembly and Handover
Our professional team oversees the assembly on-site, ensuring everything is efficiently put together. The quick, simplified build process reduces construction time and costs, allowing you to meet deadlines and move on to the next phase faster.
At Deepblue we recognize that the success of any project requires a clear understanding of the client’s requirements. We strive to build strong collaborative relationships with clients to provide open, two-way communication as well as one-stop solution. This contributes to your project being delivered on time and within budget.
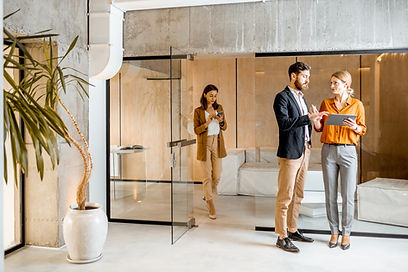
Option 2:
Custom Homes Based on Your Drawings
Initial Meeting or Communication
Architectural Design & Engineering drawing
Client Choices
We arrange a meeting or communication to discuss the project and understand our clients ideas, aspirations and expectations. We will ensure they have a clear understanding of the process and how we will work with them.
We can make architecutural design for clients, also can make structural drawing based on clients’ architectural drawing, as well as engineering calculations for the project.
We guide our clients through the decision making process to enable us to procure and order each element of the project. We can help guide you through the process of specifying and designing your home.
Producation & Procurement
Construction
Customer Care
We have a new large processing center and modern production workshop to ensure the accuracy of the production equipment and maintain high quality control.
All light gauge steel framing will be assembled in the factory, saving your time and labor cost. We can purchase all kinds of building materials for our system.
We will provide detailed installation instructions, including the assembly of light steel structural blocks, the installation of light steel on the foundation, and the assembly of various plates. We also offer our client to find builders or supervisors to construct our homes on site.
Our dedicated Customer Care Team is on hand to assist you and your property for 1 year post-completion.
As long as you become our customer, we will always provide you service with enthusiasm and professionalism.
-
Can you tell me more about your building system and technology?Our building system is based on cold formed steel (CFS) framing, which is a lightweight, strong, and durable material that can be easily shaped and assembled into various structures. CFS framing is ideal for low rise buildings, as it offers many advantages over traditional materials such as wood or concrete, such as: • Faster and easier construction • Higher quality and precision • Greater design flexibility and customization • Lower cost and maintenance • Better performance and safety • Reduced environmental impact Our technology is what makes our building system truly innovative and efficient. We use advanced software and hardware to automate and integrate every step of the building process, from design and engineering, to manufacturing and installation. Our technology includes: • Digital architectural & structural design software that allows us to create 3D models and drawings of any building type and style, and optimize them for CFS framing. • Full panelized manufacturing equipment that uses CNC machines to cut, bend, punch, and assemble CFS frames into ready-to-install panels, with high accuracy and quality control. • On-site installation tools and methods that enable us to erect the panels quickly and safely, with minimal waste and disruption. • DEEPBLUE SMARTHOUSE operating system that connects all the software and hardware components together, and provides real-time data and feedback throughout the project lifecycle. With our building system and technology, we can deliver any kind of low rise building for residential and commercial use, such as houses, townhouses, Adu, park-home, Granny flat, bungalows, villas, homes Tiny homes, Manufactured homes, prefab homes etc.
-
Can you tell me more about your design and engineering services?Our design and engineering services are part of our turnkey offering, which means we provide them in-house, without outsourcing or subcontracting to any third parties. We have a team of experienced and qualified architects, engineers, and designers since 2009, who use our advanced software to create 3D models and drawings of your project, and optimize them for CFS framing. Our design and engineering services include: • Architectural design: We can create any building type and style, from traditional to modern, and customize it to your preferences and requirements. We can also provide you with various design options and alternatives, and help you choose the best one for your project. • Structural engineering: We can design and calculate the structural system and components of your building, such as the CFS frames, panels, connections, foundations, etc., and ensure they meet the local codes and standards. We can also provide you with structural analysis and testing reports, and stamp them with our professional engineer's seal. • Shop drawings: We can produce detailed and accurate shop drawings for your project, which show the dimensions, specifications, and instructions for the manufacturing and installation of the CFS frames and panels. • Installation instructions: We can provide you with clear and comprehensive installation instructions for your project, which guide you step by step on how to erect the CFS frames and panels on site, using proper tools and equipment. We can also provide you with troubleshooting tips, safety precautions, quality checklists, etc., for your convenience.
-
How do you ensure the quality and safety of your manufacturing and installation process?We take quality and safety very seriously at DEEPBLUE SMARTHOUSE, and we have strict standards and procedures to ensure our manufacturing and installation process meets the highest requirements. Here are some of the ways we ensure the quality and safety of our manufacturing and installation process: • We use high-quality steel coils that are certified by international standards and comply with local codes and regulations. • We use advanced CNC machines that are calibrated and maintained regularly to ensure high accuracy and consistency of the CFS frames and panels. • We have a dedicated quality control team that inspects every CFS frame and panel before, during, and after the manufacturing process, using various tools and methods such as visual inspection, dimensional measurement, load testing, and welding inspection. • We have a comprehensive quality management system based on ISO9001 that records and tracks every CFS frame and panel from the raw material to the final product, and provides real-time data and feedback to our engineers and managers. • We have a customer service team that provides after-sales support and warranty for our products, and responds to any issues or complaints promptly and effectively. We are proud of our quality and safety record, and we are always looking for ways to improve our products and services. If you have any feedback or suggestions, please feel free to share them with us.
-
How long does it take to get a quote and a proposal from you?It usually takes us less than ONE week to get back to you with a quote and a proposal for your project, after you fill out the online inquiry form or contact us by phone or email. We use our advanced software to create a 3D model and a cost estimate for your project, based on the information you provide. We also use our software to generate a preliminary design proposal for your project, which shows you how your building will look like and what features and specifications it will have. We try to make our quote and proposal as accurate and detailed as possible, but they are subject to change depending on the final design and contract.
-
How does CFS framing compare to traditional materials like wood or concrete?CFS framing has many advantages over traditional materials like wood or concrete, especially for low rise buildings. Here are some of the main benefits of CFS framing: • Faster and easier construction: CFS frames are prefabricated in our factory and delivered to the site as ready-to-install panels, which reduces the construction time and labor by up to 50%. CFS frames are also lighter and easier to handle than wood or concrete, which simplifies the transportation and installation process. • Higher quality and precision: CFS frames are manufactured using CNC machines that ensure high accuracy and consistency. CFS frames are also resistant to warping, shrinking, cracking, rotting, or termite damage, unlike wood. CFS frames also have better dimensional stability and strength than wood or concrete, which means they can withstand higher loads and stresses without deformation or failure. • Greater design flexibility and customization: CFS frames can be easily shaped and assembled into various configurations and geometries, which allows us to create any building type and style, from traditional to modern. CFS frames also have a smaller cross-section than wood or concrete, which means they can create larger spans and openings, and allow more natural light and ventilation into the building. • Lower cost and maintenance: CFS frames are more cost-effective than wood or concrete, as they require less material, labor, and equipment. CFS frames also have lower maintenance costs, as they do not need painting, sealing, or treating like wood. CFS frames also have a longer lifespan than wood or concrete, as they do not deteriorate or corrode over time. • Better performance and safety: CFS frames have superior thermal and acoustic insulation properties than wood or concrete, which means they can provide better comfort and energy efficiency for the occupants. CFS frames are also non-combustible and fire-resistant, unlike wood. CFS frames also have higher seismic and wind resistance than wood or concrete, which means they can withstand natural disasters better. • Reduced environmental impact: CFS frames are more eco-friendly than wood or concrete, as they are made from recycled steel that can be recycled again at the end of its life. CFS frames also produce less waste and emissions during manufacturing and installation, as they are prefabricated in our factory and require less cutting and drilling on site. CFS frames also have a lower carbon footprint than wood or concrete, as they use less energy and resources during production and operation.
-
How do I get started with my project using your system?Getting started with your project using our system is very easy and fast. You just need to follow these simple steps: • Contact us by filling out the online inquiry form on our website, or by calling or emailing us directly. We will assign a dedicated sales representative to your project, who will be your main point of contact throughout the process. • Provide us with some basic information about your project, such as the floor plan, location, and budget of your project. You can also share with us any design ideas or preferences you may have, such as the style, layout, or features of your building. • Receive a free quote with/without a preliminary design proposal from us within 24 hours. We will use our advanced software to create a 3D model and a cost estimate for your project, based on the information you provided. You can review the quote and the proposal, and give us your feedback or suggestions. • Finalize the design and the contract with us. Once you are satisfied with the quote and the proposal, we will work with you to finalize the design details and specifications for your project, and sign a formal contract with you. We will also assist you with obtaining the necessary permits and approvals for your project from the local authorities. • Start the manufacturing process. After the contract is signed and the permits are obtained, we will start the manufacturing process in our factory, and schedule the delivery dates for your project. We will keep you updated on the progress and status of your project, and coordinate with you for any site preparation or logistics issues. • Enjoy your new building. We will assist your team throughout the installation process until it is finished and the quality is checked. We will also provide after-sales support and warranty for your new building. You can relax and enjoy your new building with confidence. We hope this explains how to get started with your project using our system. If you are ready to start your project with us, please contact us today. We look forward to hearing from you soon.
-
How long does it take to manufacture and install a building with your system?The manufacturing and installation time of a building with our system depends on various factors, such as the size, complexity, and location of the project. However, in general, our system can significantly reduce the construction time compared to traditional methods, by up to 60%. For example, a typical single-story house with our system can be manufactured in our factory in about 5 days, and installed on site in about 50days. A typical two-story townhouse with our system can be manufactured in our factory in about 10 days, and installed on site in about 70 days. A typical three-story apartment building with our system can be manufactured in our factory in about 10 days, and installed on site in about 90 days. Those numbers are based on a 6-worker team. These are approximate estimates based on our previous projects, and they may vary depending on the specific requirements and conditions of each project. If you want to get a more accurate estimate for your project, please contact us and provide us with some basic information, such as the floor plan, location, and budget of your project. We will be happy to provide you with a free quote and a detailed timeline for your project.
-
What kind of software do you use for your design and engineering services?We use a variety of software for our design and engineering services, depending on the type and complexity of the project. Some of the software we use are: • SketchUp: This is a 3D modeling software that we use to create the initial concept and design of your project, and to show you how it will look like in reality. We can also use SketchUp to create various design options and alternatives, and to make revisions and modifications based on your feedback. • Revit: This is a BIM (Building Information Modeling) software that we use to create the detailed architectural and structural design of your project, and to optimize it for CFS framing. We can also use Revit to perform structural analysis and testing, and to generate shop drawings and material lists for your project. • FrameCAD: This is a CFS framing software that we use to create the CFS frames and panels for your project, and to calculate the dimensions, specifications, and instructions for the manufacturing and installation of them. We can also use FrameCAD to connect with our CNC machines and our DEEPBLUE SMARTHOUSE operating system, and to provide real-time data and feedback for your project. These are some of the main software we use for our design and engineering services, but we also use other software as needed, such as AutoCAD, Photoshop, etc. We are always updating and upgrading our software to keep up with the latest technology and industry standards. We hope this answers your question. If you have any questions or concerns about our software, please let us know. We are always happy to help you.
-
What kind of information do I need to provide for the online inquiry form?The online inquiry form is a simple and convenient way to contact us and get a quote for your project. You only need to provide the following information for the online inquiry form: • Your name and contact details, such as your email address, phone number, and country or region. • The type and size of your project, such as the building type (house, townhouse, apartment, etc.), the number of bedrooms and bathrooms, the total floor area, and the number of stories. • The location and site conditions of your project, such as the city, state, or province, the climate zone, the soil type, and the slope or flatness of the land. • The budget and timeline of your project, such as the estimated total cost, the expected start and completion dates, and the preferred payment method. • Any additional comments or questions you may have about your project, such as the design style, layout, features, or requirements of your building. You can fill out the online inquiry form on our website by clicking on the "Get a Quote" button on the top right corner. It will only take you a few minutes to complete the form, and we will get back to you within 24 hours and the a free quote and a preliminary design proposal for your project will be sent within 5days. We hope this answers your question. If you have any difficulty filling out the online inquiry form, or if you prefer to contact us by phone or email, please let us know. We are always happy to help you.
-
Can you tell me more about your manufacturing and installation instructions?Our manufacturing and installation process is part of our turnkey offering, which means we provide them in-house, without outsourcing or subcontracting to any third parties. We have a state-of-the-art factory and a professional installation team, who use our advanced equipment and tools to manufacture and install the CFS frames and panels for your project. Our manufacturing and installation process includes: • Manufacturing: We use CNC machines to cut, bend, punch, and assemble the CFS frames and panels for your project, based on the shop drawings and instructions generated by our software. We also apply the exterior and interior finishes and fittings to the panels, such as cladding, insulation, windows, doors, etc., in our factory. We then label and pack the panels according to the installation sequence, and load them onto trucks for delivery to your site. • Installation instructions: the installation instructions and drawings provided by us. We also pre-punch the services holes for the plumbing, electrical, and HVAC systems to the panels. Our manufacturing and installation instructions can significantly reduce the construction time and cost of your project, by up to 50%. It can also improve the quality and performance of your building, as it eliminates many of the errors and defects that may occur in traditional construction methods.
-
What is included in the cost of a building with your system?The cost of a building with our system includes the following items • The CFS frames and panels for the structure, roof, and floor of the building, manufactured in our factory and delivered to the site as ready-to-install products. • The exterior and interior finishes and fittings for the building, such as cladding, insulation, windows, doors, flooring, ceiling, plumbing, electrical, and HVAC systems, supplied by our curated global partners and delivered to the site as ready-to-install products. • The design and engineering services for the building, such as architectural design, structural engineering, shop drawings, and installation instructions, provided by our in-house team of experts using our advanced software. • The customer service and warranty for the building, such as after-sales support, maintenance tips, and product warranty, provided by our customer service team using our comprehensive quality management system. The cost of a building with our system does not include the following items: • The installation services for the building, such as site preparation, foundation work, panel erection, finish installation, and quality inspection, provided by our professional installation team using our proper tools and equipment. • The land acquisition and site development costs for the project, such as land purchase, site survey, soil testing, grading, landscaping, utility connections, etc., which are usually borne by the customer or the developer. • The permit and approval fees for the project, such as building permit, zoning approval, environmental assessment, fire safety inspection, etc., which are usually paid by the customer or the developer to the local authorities. • The financing and insurance costs for the project, such as loan interest, mortgage fees, property taxes, insurance premiums, etc., which are usually arranged by the customer or the developer with their financial institutions. We hope this clarifies what is included and what is not included in the cost of a building with our system. If you have any questions or concerns about the cost of your project, please let us know. We are always happy to help you find the best solution for your budget.
-
Do I need to pay anything for the online inquiry form?No, you do not need to pay anything for the online inquiry form. It is completely free and no-obligation. You can use it to contact us and get a quote for your project without any commitment or pressure. We understand that building a new home or a commercial building is a big decision and investment, and we want to make it as easy and transparent as possible for you. That is why we offer a free quote and a preliminary design proposal for your project, based on the information you provide in the online inquiry form. You can review the quote and the proposal, and decide whether you want to proceed with us or not. If you are happy with our offer, we will work with you to finalize the design and the contract for your project. If you are not satisfied with our offer, you can walk away without any penalty or obligation.
-
How do I pay for my project if I decide to proceed with you?If you decide to proceed with us, we will sign a formal contract with you, which will specify the payment terms and conditions for your project. We accept various payment methods, such as bank transfer, L/C,DDU,DDP. In general, our payment schedule is as follows: • A 10% deposit is required when the contract is signed, to confirm your order and start the design and engineering process. • A 40% payment is required before the manufacturing process is starting. • A 50% payment is required when the manufacturing process is completed We are flexible and open to negotiate the payment terms and conditions with you, depending on your project requirements and financial situation. We can also assist you with obtaining financing and insurance for your project, if needed.
-
Do you offer any discounts or promotions for your products and services?Yes, we do offer some discounts and promotions for our products and services, depending on the type and size of your project, and the time and season of your order. Here are some of the discounts and promotions we currently offer: • A 3% discount for repeat customers or referrals, as a way of saying thank you for your loyalty and trust. • A 5% discount for bulk orders or large-scale projects, as a way of rewarding you for your business and partnership. • A 7% discount for early bird orders or off-season of big projects, as a way of encouraging you to plan ahead and avoid peak demand and delays. These discounts and promotions are subject to availability and change, and they may not be combined with other offers or discounts. They are also subject to our terms and conditions, which will be specified in the contract. We hope this informs you of our discounts and promotions for our products and services. If you are interested in taking advantage of any of these offers, please contact us as soon as possible, as they may expire or run out soon. We look forward to hearing from you soon.
-
Do you have any certifications or awards for your quality and safety standards?We do have some certifications and awards for our quality and safety standards, which demonstrate our commitment and excellence in our industry. Some of the certifications and awards we have are: • ISO 9001: This is an international standard for quality management systems, which specifies the requirements for planning, implementing, monitoring, and improving the quality of our products and services. • ISO 14001: This is an international standard for environmental management systems, which specifies the requirements for identifying, managing, and reducing the environmental impact of our products and services. • OHSAS 18001: This is an international standard for occupational health and safety management systems, which specifies the requirements for ensuring the health and safety of our employees, contractors, and customers. • CE Marking: This is a certification mark that indicates conformity with health, safety, and environmental protection standards for products sold within the European Economic Area (EEA). • EN1090 is a European standard that regulates the fabrication and assembly of steel and aluminium structures, and ensures their conformity with the relevant design specifications and requirements. EN1090 certification is mandatory for any steel or aluminium structure that is intended for use in the European Union, and it demonstrates the quality, safety, and performance of your products and services. • AS/NZS 4600: This is an Australian/New Zealand standard for cold-formed steel structures, which specifies the design criteria, material properties, fabrication methods, and testing procedures for CFS frames and panels. • SGS Certification: This is a certification service provided by SGS Group, a leading inspection, verification, testing, and certification company, which verifies the quality, performance, and compliance of our products and services. • ASTM certification :This is a certification service provided by ASTM International, a global organization that develops and publishes voluntary consensus standards for materials, products, systems, and services. ASTM certification verifies that your products or services meet the ASTM standards that are relevant to your industry or application. These are some of the certifications and awards we have for our quality and safety standards, but we also have other certifications and awards from various local authorities and organizations. We are always striving to meet or exceed the expectations of our customers and stakeholders, and to uphold the highest standards of quality and safety in our industry. We hope this informs you of our certifications and awards for our quality and safety standards. If you have any questions or concerns about our certifications and awards, please let us know. We are always happy to help you.
-
When was DEEPBLUE SMARTHOUSE founded?DEEPBLUE SMARTHOUSE was founded in 2009.
-
Where is your headquarters located?Our headquarters is located in Ningbo, China.
-
What is DEEPBLUE SMARTHOUSE's core business?We specialize in providing modern prefabricated homes using light steel frame construction.
-
Which countries do you export to?We have exported homes to over 60 countries, including the USA, Australia, New Zealand, the UK, and Europe.
-
Do you offer customized services?Yes, we offer fully customizable designs to meet specific client needs.
-
Do you have international quality certifications?Yes, we are certified with ICC-ES, EN, AS/NZS, and other international standards.
-
What is DEEPBLUE SMARTHOUSE's annual output value?Our current annual output value is around 50 million USD and is expected to reach 80 million USD.
-
What products do you offer?We offer single-family homes, multi-family homes, apartments, bungalows, granny flats, ADUs, and garden studios.
-
Who are your main customer groups?Our main customers are real estate developers, builders, architects, and hospitality developers.
-
What is your company's mission?Our mission is "Building Smart House for the World," making housing more affordable, sustainable, and high-quality.
-
What is a light steel frame house?It is a prefabricated home constructed using light steel framing, offering strength, durability, and quick assembly.
-
What are the advantages of light steel frame houses?Advantages include faster construction times, lower costs, earthquake and hurricane resistance, and energy efficiency.
-
What disaster resistance features do your homes have?Our homes can withstand earthquakes up to magnitude 10 and hurricanes with wind speeds of up to 360 km/h.
-
How do light steel homes differ from traditional homes?Light steel homes are faster to construct, more environmentally friendly, and offer superior disaster resistance.
-
Can your homes be used in any climate?Yes, our homes are designed to perform well in various climates, from hot to cold, humid to dry.
-
Which national standards do your designs comply with?We comply with international standards such as ICC-ES, EN1090, AS/NZS 4600, and others.
-
Can homes be designed based on customer needs?Yes, we offer fully customizable designs tailored to specific customer requirements.
-
How earthquake-resistant are your homes?Our homes can resist earthquakes up to a magnitude of 10.
-
How strong is the hurricane resistance of your homes?Our homes can withstand hurricanes with wind speeds of up to 360 km/h.
-
Do your homes have insulation?Yes, our homes are equipped with high-performance insulation to ensure energy efficiency.
-
What types of homes do you offer?We offer single-family homes, townhouses, duplexes, bungalows, and modular homes.
-
What markets are your homes suitable for?Our homes are suitable for residential, commercial, tourism, senior living, and government housing projects.
-
Do you offer modular building systems?Yes, we offer modular building systems designed for quick on-site assembly.
-
Are your homes suitable for extreme weather conditions?Yes, our homes are built to withstand extreme weather, including high winds, heavy snow, and intense heat.
-
Are your building materials environmentally friendly?Yes, our materials are green, sustainable, and recyclable.
-
Can your homes be expanded in the future?Yes, our designs are flexible and can be expanded as needed.
-
What is the lifespan of your homes?Our homes have a lifespan of over 50 years with proper maintenance.
-
How fire-resistant are your homes?Our homes are built with fire-resistant materials to ensure safety.
-
Can your homes integrate smart home technologies?Yes, we can integrate smart home features such as security systems, lighting, and energy management.
-
Are your homes resistant to moisture and mold?Yes, our homes are designed to resist moisture, mold, and mildew.
-
How long does it take to build one of your homes?Construction times vary, but our homes can be built in as little as 3-6 months.
-
How many workers are needed to install a home?A small crew of 5-10 workers can typically complete the installation.
-
Can your homes be installed anywhere?Yes, our homes can be installed in a wide range of locations, from urban to remote areas.
-
How much construction waste is generated?Minimal waste is generated as most components are prefabricated in the factory.
-
Are special tools needed for installation?No, standard construction tools are typically sufficient for assembly.
-
Do you provide installation services?Yes, we offer on-site installation services or guidance if required.
-
What site preparation is needed?A level foundation is required, along with utilities like electricity and water access.
-
Do you provide construction guidance?Yes, we provide detailed construction manuals and on-site support if necessary.
-
Can your homes be built on varied terrain?Yes, our homes can be built on flat, hilly, or uneven terrain.
-
Can your homes be built in deserts or mountainous areas?Yes, our homes are suitable for diverse geographic conditions, including deserts and mountains.
-
Does weather affect installation times?Adverse weather can impact installation times, but prefabrication minimizes delays.
-
Do the homes require regular maintenance?Like all homes, regular maintenance is recommended for optimal performance.
-
How much do DEEPBLUE SMARTHOUSE homes cost?Pricing varies depending on design, size, and customization. Contact us for a quote.
-
How do the costs compare to traditional homes?Our homes are typically more affordable due to faster construction times and reduced material waste.
-
How is pricing determined?Pricing is based on the design, materials, labor, and transportation costs.
-
Does customization increase costs?Yes, custom designs may increase costs, but we work to provide competitive pricing.
-
What payment options are available?We accept various payment methods, including bank transfers and letters of credit.
-
Are shipping costs included in the price?Shipping is typically calculated separately based on location.
-
Do you offer financing options?Financing options vary by region. Please inquire about available options.
-
Does the price include installation?Installation costs are usually separate but can be included in a full-service package.
-
Do you offer different price tiers?Yes, we offer homes across a range of price points to meet various budgets.
-
How do your homes save on construction costs?Prefabrication reduces material waste, labor costs, and construction time.
-
Do we deliver to Europe?Yes, we regularly deliver our prefabricated homes to Europe. Our team is well-versed in handling international shipments, ensuring compliance with local regulations and standards.
-
How long does delivery take?Delivery times can vary depending on the specific order and location. On average, it takes about 8-12 weeks from the time of order confirmation to delivery in Europe, including production and shipping.
-
Are windows included in the delivery?Yes, the windows are part of the standard package for our prefabricated homes. We provide high-quality, energy-efficient windows that meet European standards.
-
Are the assembly instructions in English?Absolutely. We provide detailed assembly instructions in English, and we also offer remote support if needed during the installation process.
-
How does your supply chain ensure quality?We partner with certified suppliers and have strict quality control processes in place.
-
What logistics channels do you use?We work with trusted logistics partners to ensure efficient and safe delivery.
-
What is the delivery time for your products?Delivery times vary but are typically 6-12 weeks, depending on the project and location.
-
Can your factories handle large orders?Yes, we have the capacity for large-scale production to meet high-volume demands.
-
What is the lead time for international orders?Lead times vary but typically range from 3 to 6 months, depending on the destination.
-
Which countries do you offer export services to?We export globally, including North America, Europe, Australia, Africa, and Asia.
-
Do you work with international logistics companies?Yes, we partner with global logistics providers to ensure timely and secure shipping.
-
Are shipping costs included in the contract?Shipping costs are typically added to the final contract based on location.
-
Do you have a global distribution network?Yes, we have a robust global network to ensure efficient product delivery.
-
How do you handle damages during transportation?We offer insurance and work with logistics partners to resolve any transportation-related issues.
-
Are your building materials eco-friendly?Yes, we use sustainable, green building materials.
-
Do light steel structures save energy?Yes, our homes are energy-efficient and help reduce energy consumption.
-
Do your products support green building certifications?Yes, our homes can qualify for green building certifications such as LEED.
-
What energy efficiency standards do your homes meet?Our homes meet various international energy efficiency standards.
-
Do your products have any environmental impact?Our homes are designed to minimize environmental impact, using recyclable materials.
-
Is your production process environmentally friendly?Yes, we follow sustainable manufacturing practices to reduce waste and emissions.
-
Can your homes reduce carbon emissions?Yes, our energy-efficient designs help reduce carbon footprints.
-
Are your materials recyclable?Yes, many of our materials can be recycled at the end of their lifecycle.
-
How do your homes achieve energy savings?We use advanced insulation, energy-efficient windows, and sustainable materials to maximize energy savings.
-
Do you have a sustainability plan?Yes, sustainability is a key focus in our design, production, and building processes.
-
What design software do you use?We use advanced CAD and BIM software for precision design and engineering.
-
How large is your R&D team?Our R&D team consists of over 50 experts in design, engineering, and materials science.
-
How do you ensure product quality?We have strict quality control processes in place throughout design, production, and installation.
-
How do you ensure innovation in your products?We invest heavily in R&D and partner with leading technology companies to stay ahead in innovation.
-
Do you have patented technologies?Yes, we hold several patents related to our building systems and construction processes.
-
What smart systems can be integrated into your homes?We can integrate smart lighting, security, HVAC, and energy management systems into our homes.
-
What seismic technology do you use?Our light steel structures are engineered with advanced seismic-resistant technology.
-
What fire and thermal protection do your homes offer?Our homes use fire-resistant materials and advanced insulation for thermal protection.
-
How do you improve sound insulation?We use high-quality materials and construction techniques to enhance sound insulation.
-
What energy-saving technologies do your homes feature?Our homes include energy-efficient insulation, windows, and HVAC systems.
-
What after-sales services do you offer?We offer comprehensive after-sales support, including maintenance and repair services.
-
Do your products come with a warranty?Yes, we provide warranties on our materials and construction, with terms varying by product.
-
What is the response time for after-sales service?Our response time depends on the location but typically ranges from 24 to 48 hours.
-
How do you handle product issues?We provide customer support to troubleshoot and resolve any issues that arise.
-
Do you offer global after-sales support?Yes, we offer after-sales support in all countries where we have sold our products.
-
Do you offer replacement parts?Yes, we provide replacement parts for all our products.
-
What are the maintenance costs for your homes?Maintenance costs are low due to the durability and quality of our materials.
-
Do you offer periodic maintenance services?Yes, we offer maintenance packages to ensure the longevity and performance of your home.
-
How can I become your dealer?You can contact us to inquire about dealership opportunities and requirements.
-
What are the requirements for becoming a dealer?Dealers must have experience in the construction or real estate industry and meet our sales targets.
-
What support do dealers receive?We provide extensive training, marketing support, and access to our product catalog.
-
Do you provide training for your partners?Yes, we offer training programs for dealers and partners to ensure product knowledge and sales success.
-
How do dealers get sales support?Dealers receive ongoing sales support, including marketing materials, technical assistance, and lead generation.
-
What product lines can dealers sell?Dealers can sell our full range of prefabricated homes, modular buildings, and light steel structures.
-
Can dealers offer customized products?Yes, our dealers can offer customized solutions based on customer needs.
-
What partnership models do you offer?We offer various partnership models, including dealership and distribution agreements.
-
Can dealers provide installation services to customers?Yes, dealers can either provide installation services directly or partner with local contractors.
-
Do dealers receive marketing support from DEEPBLUE SMARTHOUSE?Yes, we offer marketing support, including co-branded materials, online promotion, and local market insights.
Request a Consultation
Contact our specialists today to find out how we can work together on your project needs.